Written By Bobby. On Jan 03. In Shop Systems

Once you establish your design and procedures, it’s pretty much rinse and repeat after that; all joints are installed the same way.
“Installing a permanent dust collection system is too hard so I just use flex duct and connect it to the machine I’m using”. Sound familiar? Well that’s how a lot of woodworkers think, not feeling like an HVAC expert or very interested in dealing with sheet metal ductwork. But I bet you’d like to have a dream dust collection system in your woodshop.
But, if you just know the basics (do’s and don’ts, how to size the ducts and the collector), you pretty much can buy the pieces you need and put it together like Legos and be done.
You also don’t have to do it all at once; of course design for the whole shop first but you can always run enough duct to catch a few important machines and do the rest as you have time.
The time benefits alone are worth the brief learning curve effort. You’ll no longer have to hook and unhook flex hose from the machine you’re about to turn on, turn on the dust collector, then the tool. You’ll just have to open the blastgate, and hit “ON” using your keychain remote.
Having a central dust collector in one place (or two, one for each side of a larger shop) is a much better solution than either using a shop vac rigged with a mini-cyclone or bucket separator trying to mimic a full sized collector, or an undersized 1HP collector rolled from tool to tool.
There’s a reason professional shops have a centralized dust collector system; it’s much more convenient and efficient, and safer for those doing the woodworking.

I prefer sheet metal ductwork; there’s only a slight learning curve. It gets rid of any fears of static electrical dust fire fears, and I think looks cooler too.
Sheet Metal vs. PVC Ductwork
This is a source of a lot of forum discussions/ arguments and some blog articles. Basically it comes down to safety concerns of static electricity build-up caused by dust rubbing against PVC piping.
If you have a benchtop planer with a flex hose attached to the dust collection port, you’ve probably gotten a shock from touching it while it was drawing chips. I’m always surprised by how much of a shock dust moving through a non-metal tube can be. This electricity can cause dust fires/ explosions with the right dust-air mixture of dust that exists inside the ductwork. With the proper ratio of dust to air, it is well known this can cause a disaster.
However, it is often argued that in a typical small shop, the relatively small amount of dust isn’t much of a danger. Some people use a PVC duct system combined with grounding wire routed alongside (coiled outside and run inside) the piping to help mitigate any static electricity build-up.
For me, while it may be safe to use PVC, I’d rather just use sheet metal ductwork and not worry about it. The reason people are tempted to use PVC is that it’s easy to deal with (just like sprinkler pipe but on a larger scale), the piping is smooth on the inside surface, and it’s pretty cheap to buy.
I’ve found, however, that sheet metal ductwork is fairly simple to install (if you can figure out how to build furniture you totally can learn this), and not really that bad expense-wise. You can design the whole thing and install sections at a time as funds allow.

Choose the right fittings for more airflow; there are a lot of restrictions already in a dust collection system so why make it worse by choosing the cheap ones? With the high air velocites the static pressure losses are magnified much more than in a slower-velocity air conditioning system
Basic Components (Your Legos to Buy)
Once I had the duct routing in mind (see the Dust Collection Mastery article for more on this), I knew I had to go shopping for all the parts. Just going to Rockler, hopping on Amazon or the Penn State Industries website isn’t enough; you want know what you’re looking for and narrow your buy list. Trust me, you only need a fraction of all that’s available.
I like to just start at a typical tool, and work my way back to the dust collector and list the items I’ll need.
The parts list might look something like this:
- Dust hood or machine dust port, sized hopefully the same as the duct run back to the collector (if not, you can replace the original to upsize)
- Approx. 6 ft. of flex hose to get from the tool port to the blastgate
- Bridging hose clamp to connect the flex hose to the machine dust port
- Blastgate, sized for the diameter of duct (I like the metal ones)
- Bridging hose clamp to connect the flexhose to the blastgate
- Some snap-lock straight duct connected to the blastgate (this is your branch duct)
- Sheet metal screws (I like the hex-head ones because the driver doesn’t tend to slip) to attach the sheet metal duct to the blastgate
- Foil tape (should be UL-181 approved/ labeled) to seal the sheet metal connections
- A 1.5 radius (long radius) elbow(s)
- Duct sealant (brush-on type) to seal the elbow seams and the joint connections
- Some more straight duct to get the main run back to the dust collector
- A Wye-fitting to connect the branch duct to the main duct
- Main duct, all sized the same diameter as your branch duct if you use one machine at a time
- Main duct vertical riser (“drop”) down to your collector’s inlet
- Short bit of flex duct so you can roll your collector a few feet in any direction, and to help avoid duct joint separation during bag-emptying
- 6 duct diameters worth of straight duct directly into your collector’s fan intake to reduce “system effect” pressure losses (basically your goal is 6 duct diameters worth of duct length, i.e. an elbow fitting right into your fan intake = bad)
- Duct transition, if necessary to convert your pre-calculated ductwork diameter to the fan intake size that came with your dust collector (don’t assume this inlet size is the “answer” to what size ductwork you really need for your overall system)
- Duct Supports for hanging ceiling ductwork and restraining duct drops down from the ceiling (where the flex hose attaches to the blastgate)
- Optional duct silencer at the discharge side of your fan to absorb some fan noise
- Floor sweep if you want a floor-mounted port to sweep chips into; make sure you put a wire mesh screen to prevent large chunks of wood (like tenon offcuts or dovetail bits), and a row of rare-earth magnets at the inlet to catch metal such as stray fasteners, which can spark against your blower impeller and cause a fire or damage the blades
- Clean-outs which will allow you to access different parts of the system to clear clogs; they sell duct access doors or you can use a wye-fitting to create a small capped branch that you can open and clean a ball of shavings blocking airflow
- Grounding Wire to create electrical continuity between the flex duct and the tool
Then there are few tools a typical woodworker may not have but will need:
- Crimping Tool for shaping the ends of duct joints for a slip fit
- Tin Snips for cutting the sheet metal (wear gloves when handling)
- Hex driver bit for your drill to drive the fasteners

These crimpers allow you to fit the ducts together; just remember to point the crimped end toward the airflow.
By diagramming it out, even if it’s just a hand-sketch, will help you count the # of each component you need.
For example, while shopping, it’s better to have a list that says “(4) 6” diameter 1.5 radius elbows, (6) bridging hose clamps, 6” diam., (2) wye-fittings at 6”x6”x6”, etc.” rather than have to try to think while in the store. Inevitably you’ll forget something and lose momentum during the assembly.
Which Types of Components to Choose
Each of the above components have several options associated with them. I’ll break down the most common choices available, and explain my choices.
Dust Hood/ Ports:
- Just use the one that came with your machine, or
- Buy/ make one to match the duct diameter that you calculated
If you calculated that you need 5” ductwork, but your jointer came with a 4” dust port, I strongly suggest you either buy or make a replacement dust hood/ port that matches the duct diameter. This will reduce the static pressure (resistance to airflow) and will result in more CFM, which will help collect finer dust particles. I also find that larger shavings clog up the 4” jointer port anyway.
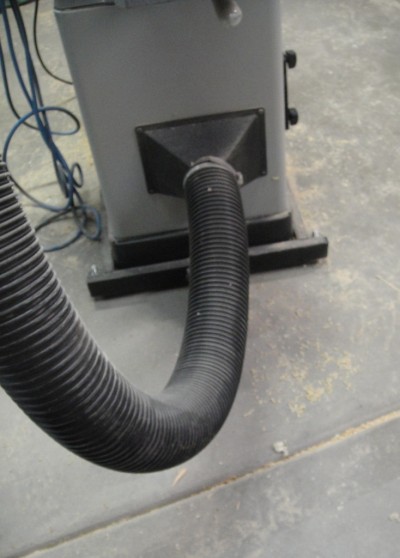
The Jointer I have comes with a 4” dust port but I find that it clogs with shavings. Plus, it’s not getting close enough to the recommended CFM because of the higher static pressure the smaller diameter flex hose has.
Hose Clamps:
- Straight metal strap, either hex bolt type or keyed screw closure, or
- Bridging hose clamp, which offsets or “bridges” over the flex hose ridges for a tighter, more continuous clamping seal between the flex hose and whatever it’s seated over
I’ve known about these bridging hose clamps for awhile but I finally just bought some. My goal is to limit the leakage from the system to make sure the suction is focused on the dust port. Most people don’t think of the flex hose connection as a leak source but it is, and due to the normal hose clamps not applying evenly distributed pressure.
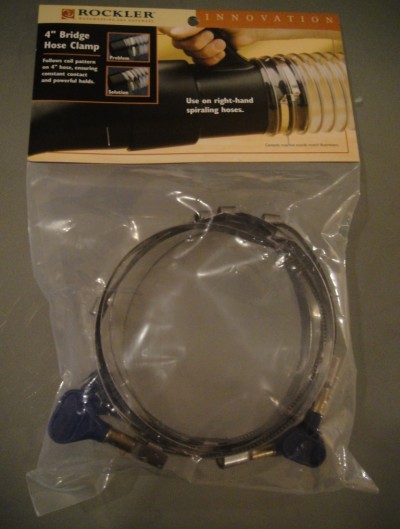
Bridging hose clamps are better than conventional ones; however these clamps from Rockler work on right-hand swirled flex. If you have left-hand, you’ll need to make sure that the clamps are bent the right way.
Blastgates:
- Cheap plastic ones, or
- Cast aluminum type
I like things that will take my abuse so I got the aluminum ones, with the cast aluminum body and hex nut to hold it in either open, partially open, or closed position. You can get the plastic kind but I don’t think you’re saving that much money. Some of these are “self cleaning” in that the sliding gate goes all the way through the body to push out accumulated dust. Just make sure that whichever one you get will minimize leakage when closed. I added some foil tape to the body to help with that Make sure the air suction, when closed, pulls the metal gate in the same direction that the locking screw pushes on it for a better seal. Are your blastgates facing the right way?
Straight Duct:
- Straight lock-seam, sometimes called “snap lock” type, or
- Spiral seam ductwork, or
- Norfab ductwork with connection clamps, specially shaped ends for easy but removable connections
I buy the longitudinal seamed straight duct that snaps together, and just seal the seam with duct mastic.
Spiral seamed ducts are made on a machine that makes the longitudinal seam wrap around the duct. These are stiffer and have a lower likelihood of leakage, but more expensive. You’ll often see them in commercial buildings, especially exposed ceilings.
Also, when it comes to the sheet metal thickness (“gauge”), the higher the gauge number the thinner it is. I buy 30 gauge and it’s been perfectly fine for my collector (nothing collapses, even with gates closed), but you may want a higher gauge depending on the static pressure your dust collector can generate. 3hp cyclones may require a higher gauge. You can look online for what static pressure (look for negative pressure) each type can take.
You don’t want to start the collector with all the blastgates closed and wind up with collapsed ductwork…it really can happen. You can install a spring-loaded “safety damper” that you can make yourself. You can use trial and error on the spring tension such that it stays closed with any one blastgate open but if you accidentally close all of them then this spring damper will open to relieve the excess vacuum inside the ductwork.

Snap-lock ductwork is easy to work with, including cutting. All you have to do is crimp one end, connect to the right fittings with sheet metal screws, and seal the seams with duct mastic.
Sheet Metal Screws:
- You can get regular sheet metal screws, or
- Self-drilling sheet metal screws
You can also choose between:
- Phillips head, or
- Hex head (or both…see photo below)
Due to the overall inexpensive nature of fasteners, it’d just be silly to not get the best and most convenient ones available. To me, that means hex-head self-drilling. When installing the ductwork, you’re often on a ladder holding the ductwork with one hand and trying to hold the drill/ driver in the other.
The hex head can be held by the hex driver without falling out and doesn’t tend to slip like a Phillips head will often do. Then, with no need to drill a pilot hole, switch to a driver bit and then drive the screw. The self-drilling screws allow you to just push against the sheet metal while spinning it and it’ll go through the sheet metal and drive tight in one step. I always brush sealant over each screw when I’m done with the basic assembly.
Foil Tape:
- Regular foil tape, or
- UL-181 approved foil tape
Most of you know that “duct tape” isn’t really for ductwork. The adhesive isn’t meant for the temperature variations in HVAC heating and cooling ducts, and it eventually falls off. This will especially happen in a hot garage, humid basement, or hot attic space. They do sell duct-tape like products that are UL listed for ductwork, but the best thing to use is foil tape.
They sell “general use” foil tape, but the UL-181 is approved for HVAC ductwork. It’s a few dollars more but I think it’s worth not having to worry about it pealing off over time; I’ve experienced it when I made my insulated garage door panels. There are several UL-181 classifications (flex duct, fiberglass duct, etc.) but generally by getting this kind of tape you know it’s good for temperature variations, which you probably have in your shop.
I use foil tape to cover seams (usually the ones I may want to disassemble in the future), blastgate seams, and cleanouts.
Duct Sealant:
- Silicone caulking, or
- Duct Sealant
Some people use regular caulking to seal the joints, but that can be messy and difficult to apply. I use duct sealant (mastic) which is designed to be brushed onto seams and fill all the gaps. It comes in small bucket containers or caulking tubes.
I like to brush on the majority of it at the workbench to complete subassemblies, then do a “final seal” once it’s all installed in the permanent location. This is because you can break the seal by moving the ductwork around. Make sure you clean and degrease the ducts before applying sealant or it won’t stick as well. Acetone is fine for that.
Wye-Fittings:
- Tee fittings, or
- Real Wye fittings, preferably 30 degree
Generally, ductwork configuration for best airflow is fairly intuitive. For example, having the branches tie into the main run at an angle towards the airflow is just smart, rather than a direct side-tap. You reduce your static pressure losses (resistance to airflow) by using wye-fittings rather than tee-fittings. 30 degree or 45 degree branch angles are available, but I like the ones that angle more in line with the main run, for obvious reasons.

I use wye-fittings for all branches from the main; I added a few for future tools I plan to buy. They’re just capped for now.
Elbows:
- 1.0 R/D Standard Radius Elbows, or
- 1.5 R/D Long Radius Elbows, or
- 2.0 R/D Long Radius Elbows
You can really ease up the resistance to airflow by making the turns more “sweeping” and gentle. Less static pressure loss means more CFM at the tool, which is critical for fine dust extraction.
Most elbows are 1.0 R/D, which just means that the radius of the turn is equal to the radius of the duct diameter. The higher this ratio the more gentle the sweep is. I buy 1.5 R/D, but I still have some 1.0 R/D that I intend to replace.
You can also choose between:
- Stamped elbows, or
- Gore-type adjustable elbows
Die-stamped elbows are smooth inside, but you’re locked into an exactly 90 degree turn. Inevitably your walls aren’t plumb or square so having some leeway (adjustability) is nice.
Plus, with some machine drops or other offsets you need to create, the adjustability of a 4-gore or 5-gore elbow is necessary. These are just segmented elbows that rotate relative to each other to make angles other than 90 deg,, and allow you to make the inlet and outlet at odd non-perpendicular planes.
The only drawback you get is there are more seams in this elbow, so you need to seal them well. They are prone to sliding and breaking the seal so you can either foil tape them, or just brush on sealant when you’re all set. On larger ductwork, you’ll often see the contractor apply sheet metal strap along the elbow to hold the segments in place, then seal the whole thing.
So once you’ve bought all the “Legos”, it’ll probably take an afternoon’s worth of time to put it all together.

By using long-radius elbows, you give the air a gentle sweep to travel in, reducing static pressure (resistance to airflow), and you get more airflow (CFM) out of it.
Designing Your System
While designing your dust collection system, you should make the above choices so you account for them in how everything fits together. By drawing your ductwork to scale, it’ll give you an idea of how many feet of straight duct you’ll need.
My first design made assumptions about my dust collector’s CFM/ Static Pressure capability. Now I’ve developed a calculation spreadsheet with true engineering fluid dynamics formulas and minimized “rules of thumb”. I also bought an anemometer so that I can actually measure my airflow both in the main and at each tool.
By being able to predict the airflow, I can decide on what diameter of ductwork to design around. I have to also be careful that the ductwork isn’t too big for the CFM I’ll be getting or the velocity will be too slow to carry chips back to the dust collector. If the diameter is too small, then you’re going to have a higher static pressure loss and therefore less CFM at the tool.
Your goal should be to minimize static pressure losses in the system and maximize the CFM available at each tool, all while maintaining the minimum recommended velocities in the ductwork.
Below is my original dust collection layout. Right now, I’m in the process of re-calculating the whole thing knowing my actual airflows and being able to predict my static pressure losses with various duct diameters and CFM values. So, my ductwork sizing might change from that, but the layout will be pretty much the same.
Click here for the woodworking plans: Dust Collection Plan
WoodChip Tip: If you’re running one machine at a time, there’s NO reason to have your branch ducts sized less than the main duct. I originally had my main duct at 5” and branch ducts at 4”, mostly for convenience due to most dust ports and flex hose being 4”. But, as an engineer I know better. So, when I finish my calculations I will go through the trouble of finding odd-sized flex hose, blast gates, and tool ports if that’s what the calculation indicates is best.
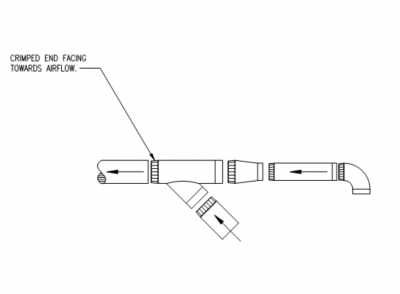
Once you’ve put all the fittings on the floor or bench facing the right direction, you can mark the correct side to crimp, so you don’t accidentally have it face against the airflow direction.

Configuration for fitting ductwork together; all you need is some duct crimpers and self-tapping sheet metal screws.
Some Things I Learned Installing My System
I installed my first system in my Ladera Ranch house, where I had a single-car garage as the workshop. I just read a lot about how to install sheet metal ductwork and dove right in. I bought whatever they had at the home center, and pretty much figured it’s good enough. It worked but was far from ideal.
However, now I’m willing to buy some components online so that I get exactly what I need, and buy the readily available parts at the home center.
Here are some things I’ve learned.
- Silicone sealant is a pain to deal with, and can’t be painted easily, whereas real duct sealant can
- Phillips head sheet metal screws are difficult to drive one-handed without falling or slipping; make sure it has a hex head
- Duct drops down to machines need to be restrained due to the flex hoses tugging on them to prevent the sealed seams from breaking
- 4” tool connection at the jointer tends to get clogged with shavings, so maybe upsizing this is a good idea, if velocities permit
- Minimizing flex hose is really good for static pressure; I measured the difference and it’s huge. Have just enough flex hose to move the machine around a few feet.
- Place the rigid sheet metal duct drop with its blastgate as close to the machine as you can without the flex hose interfering with the infeed or outfeed.
- Minimum 3 screws per duct joint is needed to prevent it from coming apart; I use 4 at joints under higher stress such as flex hose branches.
- Using the crimping tool to crimp the male end of a duct joint, make sure that it goes toward the airflow (remember air flows away from the tool back to the collector)
- When laying out the elbows, face the crimped end toward the collector (in the same direction as the airflow)
- It’s good practice to run a grounding wire from your machine around / inside the flex hose to the sheet metal duct to keep the system grounded. This will help mitigate dangers of static electricity vs. dust clouds.
- Rolls of sheet metal hanger strapping is the most convenient way to suspend the ductwork, although they do sell specialty hangers so you can better restrain duct drops. Brace ducts by crossing the straps at angles.
- Lay out the pieces on the floor to prepare sub-assemblies. Put together as many parts on the ground as you can, then loosely suspend those subassemblies so they can be connected when you’re on the ladder.
- Buy like 6 feet of extra straight duct; if you buy the snaplock type don’t assemble the seam so you can return it if you don’t need it afterall.
- Pre-seal your wye fittings and straight duct while on the bench. For elbows, the individual joints move around a lot so seal those when finally installed.
Once you do the hard work of design and gathering all the parts, the installation itself is actually fun and not bad at all.
Related Articles:
My New Dust Collection Filter Bags Arrived!
Does Your Dust Collector Filter Bag Spray Fine Dust Up Your Nose?

You can either buy rolls of sheet metal strapping with holes every inch or so, or you can buy special duct hangers from your home center. I use these for portions of the ductwork under higher stress, such as where flex hose yanks on the drops when the machine is moved around.
For more guidance in assembling your Workshop Design, click on the Starting? Go Here! category and read those first.
Connect with me on Facebook, and follow me on Twitter for more ninja tips to Optimize Your Woodshop!
And, if you’re on Twitter, be sure to follow #woodchat every Wednesday night, at 6:00 pm, PST.
Gotta get more clamps,
This will be my 3rd (And I hope final) dust collection redo. I have one question. I see that most people run their main ducts overhead and drop to the machine. Although I could do this my thoughts are to run low against the wall. I have a 2hp Jet collector and it seems to me that there would be more stress to pull the air up (gravity) then down rather than down then across to the collector. Thoughts?
Bob
I feel strongly about it and really like mastering more on this subject. If feasible, as you acquire experience, would you mind updating your blog with much more information and facts? It is very helpful for me.
Good Afternoon Sr.
I’m investigating about Hanger separation recommended for dust collection systems.
We have some dust collection systems and I would like to know how to determine or what are the standards to install every hanger (separation between them). I’ve heard and saw some tables referencing to this, but, they only speak about steam and water, not dust.
Thank you!!
Jose Balderas
SMACNA or your Mechanical Code will often have have a chart based on duct sizes and shapes. SMACNA has Table 5-2 “Minimum Hanger Sizes for Round Duct”, but it starts at 10″ round. For small round duct like I have, I just strapped them every 2 ft. or so, and at junctions, resulting in spacing greater than any chart I found. You’ll have some extra weight on wye fittings due to the flex ducts and blastgates. I also tend to put some force on them when I disconnect them occasionally, so having the fitting there strapped helps. Same with corners. When designing commercially, there is a code compliance aspect to the design so following the code charts will be necessary (these include how they’re anchored as well, such as into concrete or wood, embeddment of the fasteners, what type/ size of fasteners, etc. People can get pretty crazy with that in their home shops. For me, I used construction screws (not drywall screws) and standard duct strapping and some hangers.
Do you still need to run a ground to metal ducting and if so where and how many or how often?
I don’t think you’d need a ground for metal ducting, assuming your metal is continuous. Where you have flex ducts you can run a wire to “jump” across. Many have questioned the need to ground plastic pipe, but judging by the sharp static shock I feel at my planer’s plastic flex duct I’d rather just ground any significant lengths of plastic pipe. For vibration isolation purposes, I do have a short plastic flex section near the collector, so jumping a wire across that is a good idea, and since it’s cheap and easy to do it’s not worth it to me to research how necessary it is, I just figure do it.
Your information on pvc pipe for dust collection is outdated and repeats miss information. I have used ABS and PVC piping in 2 different shops. I’ve never encountered this static electricity problem you describe running a 5hp Clear Vue dust collector.
I’ve experienced sharp static shocks from my planer’s plastic flex duct. Same with small sections of PVC I experimented with. Because grounding is so cheap and easy, I figure I’d do it. The ClearVue ductwork may be designed with materials that don’t tend to build up static charge. Now, looking around online I haven’t heard of someone’s shop blowing up where static sparks were attributed to the cause. To me it’s more annoying when I touch it or brush against the flex line. It gets hotly debated but honestly it’s so easy to run the wire that it didn’t seem worth the time to me to take the chance. I see it as a minor risk though, but it is a thing, in that a shock is produced in several types of plastic pipes.
Most excellent! You have given me solid information that I really needed. I inherited a woodshop that had been dormant for 27+ years at my school. Besides hundreds of hours in renovating, purging, and organizing, I’m learning the ins and outs of dust collection. Our system has a 4 barrel shaker bag house with 64 bags and 15hp. 14″ main trunks. I’ll have the planer, lathe, jointer, table saws all on 5″ and 6″ drops. Currently the sound level is 105db in the shop! So we are learning how to make mufflers and silence the bag house as best we can while planning runs and getting the duct work in place. It’s a ton of work, but lucky for me, I have all the metal duct work and most of the gates needed which helps relieve my fundraising concerns. Hex self drilling screws, duct sealant, and assembly advice graciously heeded! Thank you so much! Just what I needed!
How much did your system end up being? I would like to do sheet metal ductwork, but it seems it will be incredably expensive compared to flex or PVC. Am I missing something?
I don’t have a total cost, since I bought the fittings and ductwork over maybe a year or two. I got most of the straight ducts from Home Depot, and most of the fittings online. Those fittings are what cost a lot; the ducts themselves were not much. They are mostly 30 ga., which is probably the thinnest I’m comfortable with. No real need for heavier gauge unless you’re operating a 5 hp machine or something. Some people have designed a “pressure relief” damper at the end of their runs with a spring-loaded door. The idea is to make sure the suction isn’t so high that it tends to collapse the ducts. I didn’t choose PVC because I get static shocks from it (I still feel them from the plastic flex), and worried about the fire risk (however real it may be). Some people have had success with the ClearVue and other plastic/ PVC ductwork, but personally I’d ground it with wire though.
Getting back to $, the overall runs weren’t all that long. I have maybe 40′ of mains, split into two runs, some vertical 6″, and the 4″ branches. The first ducts I bought were for the “critical” machines like the Table Saw and Planer, where a lot of chips and dust is created. You can hold off and cap the mains for some other machines and just add to it over time.
Thanks for a really thorough article on dc design, setup, and some theory. Excellent resource for someone like myself just getting started in shop set up. Great site!! Thanks again.